Today’s cars and trucks are chockablock with computer chips and sensors, actuators and modules, components that are backed up by untold lines of software code. These cutting-edge parts are required to deliver the advanced safety and convenience features drivers expect, but vehicle complexity is becoming a problem, which is why supplier company Forvia has developed a new type of electrical architecture to address this looming issue.
In simple terms, the firm’s newly developed zonal modules are designed to streamline how information gets handled in a vehicle’s electrical system by pre-processing data within a geographic zone opposed to having a host of different domain controllers. This decreases the high-performance computer’s (HPC) workload and can dramatically reduce the amount of wiring needed in a car or truck, which should deliver both cost and weight savings.
SEE ALSO: You can buy a new Nissan from your couch, get special training at home, too
“As we’re thinking about all the trends, you have electrification, you have automated driving with strong connectivity, we’re putting more and more sensors in, which means more and more ECUs, more and more wiring, everything,” said Ben Cohen, head of sales excellence and marketing at Hella. “So, the idea is to make things less complex and go from basically … different domains being controlled separately to them being controlled in geographical zones.”
For example, a lower-end vehicle with few features may have only one zone module, but a flagship-caliber luxury model with all the latest and greatest amenities may have three, a front, middle and rear zone module. As Cohen explained, “[The] one in the front just can control all the domains that run in the front instead of five different things that are controlling everything.” The processing of data for advanced driver assistance features like adaptive cruise control, automatic high beams, lane-keeping assist and blind spot monitoring could all be handled by a front-mounted zone module instead of a bunch of separate controllers.
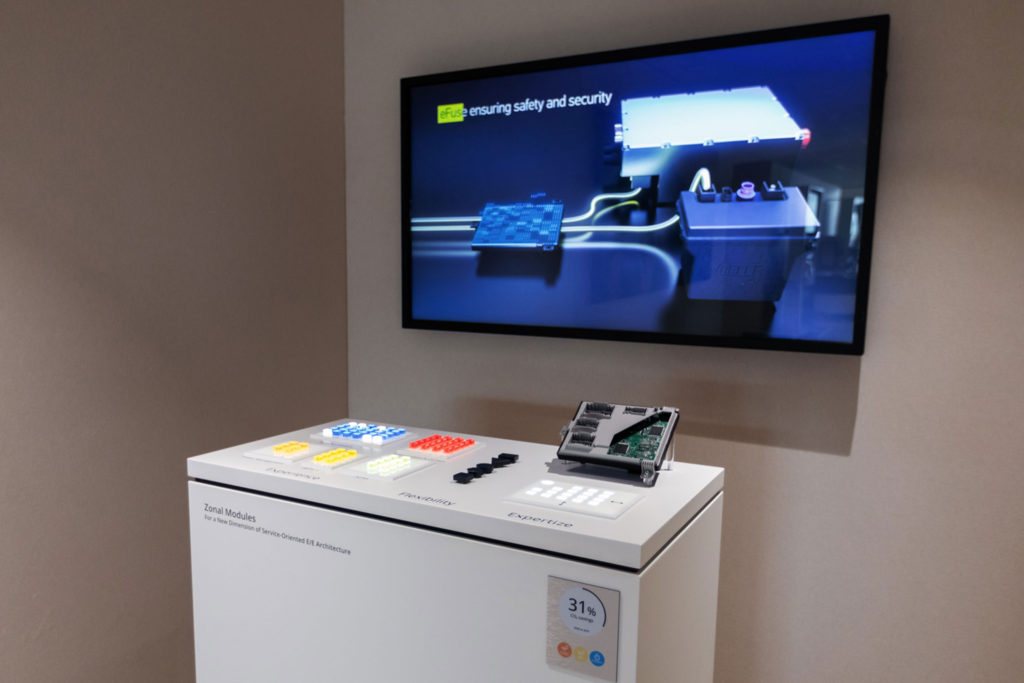
How were Forvia engineers able to consolidate so many components into just a few modules? With a smile Cohen said, “Carefully.” He explained, they have years of experience with integration, have created a lot of standards and know how to build computer boards. This expertise, along with judicious optimization, is what enabled Forvia develop this new electrical system. “[And] we’re not beholden to a specific type of sensor, we’re not beholden to a specific HPC, so it allows flexibility in the design to allow us to reduce the complexity inside of the vehicle,” he added.
Aside from weight and cost reductions, lowering complexity pays other dividends, too. Forvia’s zonal modules can also streamline vehicle engineering. “It’s reducing development time, it’s reducing the amount of pieces you need to make, it’s reducing controllers, so, lots of reduction,” added Cohen, and that is something that is sure to appeal to OEMs who are always looking to cut costs and expedite vehicle development.
CHECK THIS OUT: Ford’s high-performance Lightning concept spied in Dearborn
Forvia’s zonal modules are not in production yet, but Cohen said there’s a lot of interest from automakers. He estimated the technology will hit the road in the next three to five years, so, it’s being integrated into vehicle programs that are under development right now. “I would say it’s not if but when, so it’s coming.”