How do you maximize the interior volume of an electric vehicle? There’s a lot that can be done, like mounting the battery underneath the floor and right-sizing powertrain parts so they take up as little space as possible, but engineers at supplier company Continental have come up with another solution. Their new Electric Corner Module pushes bulky suspension and driveline components out to the very corners of a vehicle to minimize cabin intrusion.
SEE ALSO: REE Automotive has the EV chassis market ‘cornered’ thanks to its innovative drivetrain tech
As shown, this system features a trailing arm suspension design with an adjustable air spring as well as a space-saving horizontally mounted shock absorber. Motivation is provided by a super-efficient hub motor, while a so-called dry braking system, that is, a setup with no fluid or associated hydraulic lines, handles deceleration when regenerative braking is not used. Conveniently, this is another next-generation technology Continental is actively developing. Overall, the Electric Corner Module’s design is shockingly low and compact.
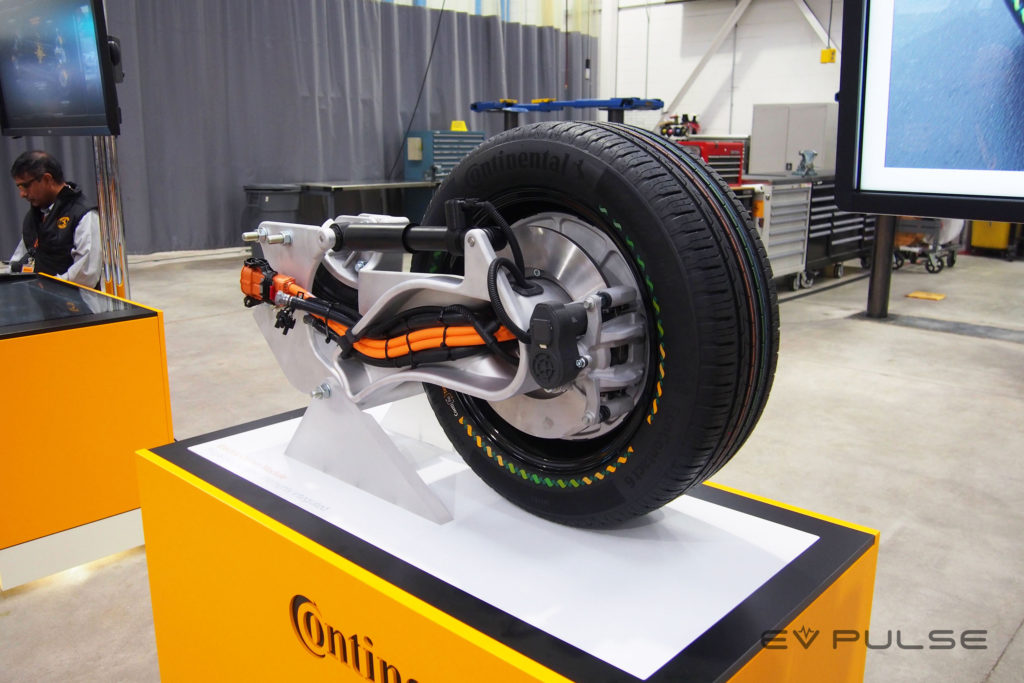
If this sounds a bit familiar, it should. The basic concept is similar to what REE Automotive is doing, though these two companies are taking wildly different approaches to reach the same destination. In comparison, REE Automotive’s corner modules mount all bulky steering and drivetrain components directly to the chassis for reduced unsprung mass, and their system features integrated steering capability.
Not to be outdone, “We are also developing a front-wheel application with steering,” noted Peter Olejnik, the man responsible for strategy and future solutions at Continental’s safety and motion business unit in North America. “But for packaging reasons it can’t be a copy, one-to-one. You need to have a slightly different design,” he added.
The benefits of Continental’s Electric Corner Module are numerous. Aside optimizing the interior volume of electric vehicles by providing greater space between the axles, this technology also improves efficiency, simplifies maintenance, increases maneuverability and since it’s basically a plug-and-play solution, makes it far easier for automakers to engineer and manufacture vehicles.
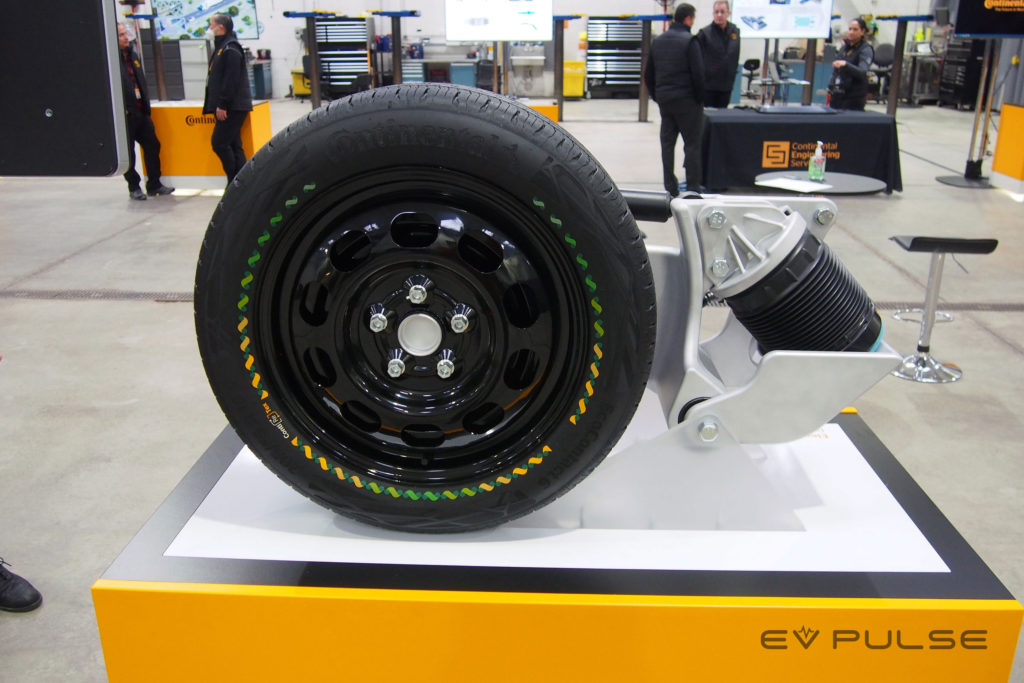
Since hub motors have no reduction gearing, there are fewer losses than other electric powertrain configurations. Olejnik explained that the company supplying these components to Continental claims that by optimizing the range where these motors typically operate, efficiency can be increased by up to 20% on the WLTP testing cycle, a massive improvement.
CHECK THIS OUT: 2024 Polestar 2 gets significant range and performance upgrades
Beyond that, hub motors provide another important benefit: improved regenerative braking. With no reduction gearing, Olejnik said you get regen almost down to zero miles per hour, which further improves vehicle efficiency.
Streamlining maintenance, the Electric Corner Module is super easy to swap out if something goes wrong. The whole assembly can then be repaired or refurbished on the workbench instead of in the vehicle. All you have to do is unbolt the unit from the vehicle, unplug a few electrical connectors and remove a couple cooling hoses. That last item could be a bit messy, but motors need to be cooled to optimize their performance and efficiency. “We can’t avoid that, unfortunately,” said Olejnik. “But other than that, it’s really a plug-and-play solution.”
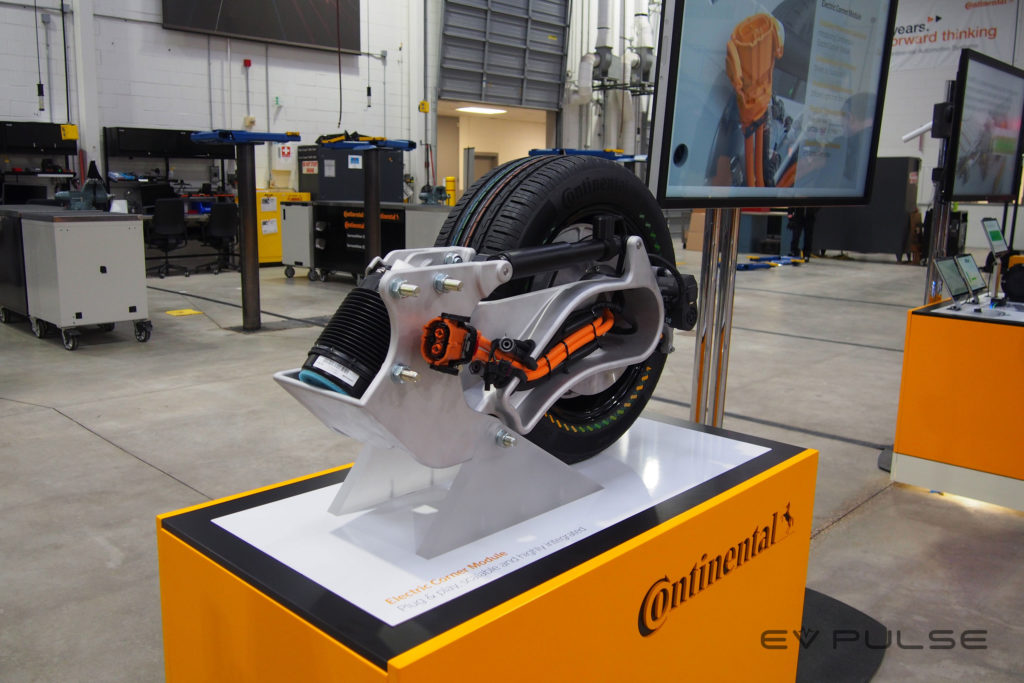
That streamlined serviceability can also make life easier for automakers. During the assembly process, once Electric Corner Modules are attached the entire chassis “can autonomously maneuver its way through the production plant” said Olejnik. “Most OEMs have that on their radar screens because you can do it. It’s really clever,” something that conceivably could reduce the complexity and cost of installing vehicle assembly lines.
At least initially, Continental is targeting small, neighborhood delivery vehicles with this drivetrain technology. Drastically increasing maneuverability, these machines may only need three wheels, which can enable them to turn around basically within their own length “similar to zero-turn lawn mowers” Olejnik said. With adjustable air springs, these vehicles could also lower themselves to make picking up or loading cargo easier.
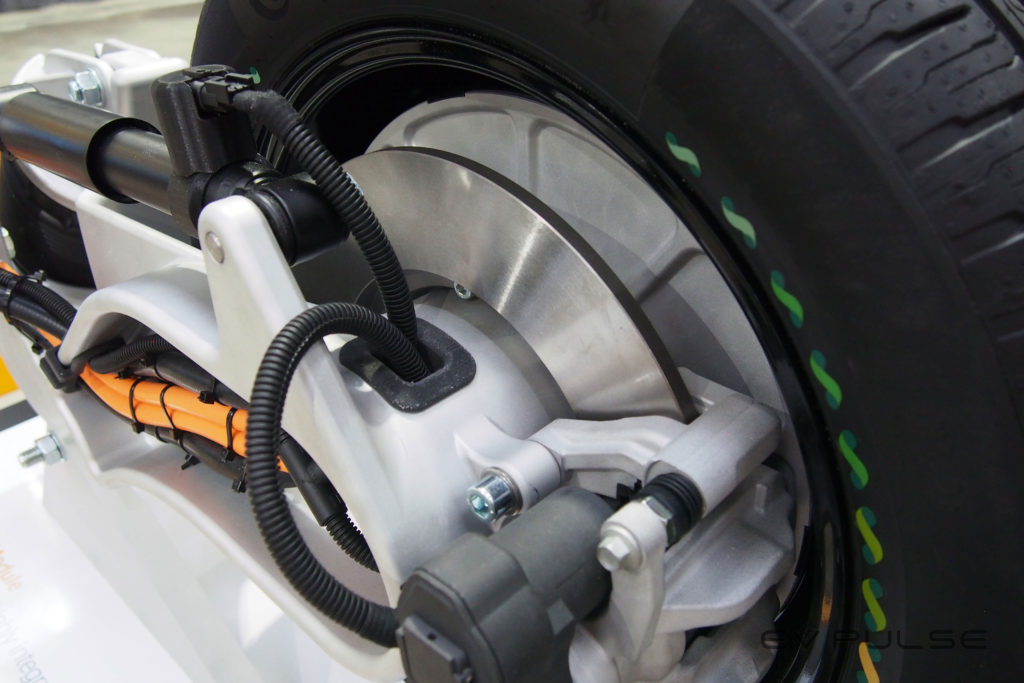
The Electric Corner Module offers many benefits for commercial applications, but passenger car manufacturers are eyeing the technology, too. “[We] initially targeted the delivery vehicles, the last-mile delivery vehicles,” said Olejnik, “But when we did the packaging studies, for various use cases we also found out that this thing, as-is, without really any additional tweaks … already fits into a pass car.” He said OEMs are requesting information on this technology for use in personal vehicles and even medium-duty trucks.
MORE GREAT TECH: High-tech drum brakes could improve EV efficiency. Yes, drum brakes
Continental’s innovative Electric Corner Module is not available in the market at this time, but automakers are interested in the technology, “A lot more than we would have thought,” according to Olejnik. Development work is still being done, but this system could easily hit the road by 2028, or even sooner if a vehicle manufacturer wishes to implement it.